Are issues with RAAC affecting your buildings?
What are the risks of RAAC and what can you do?
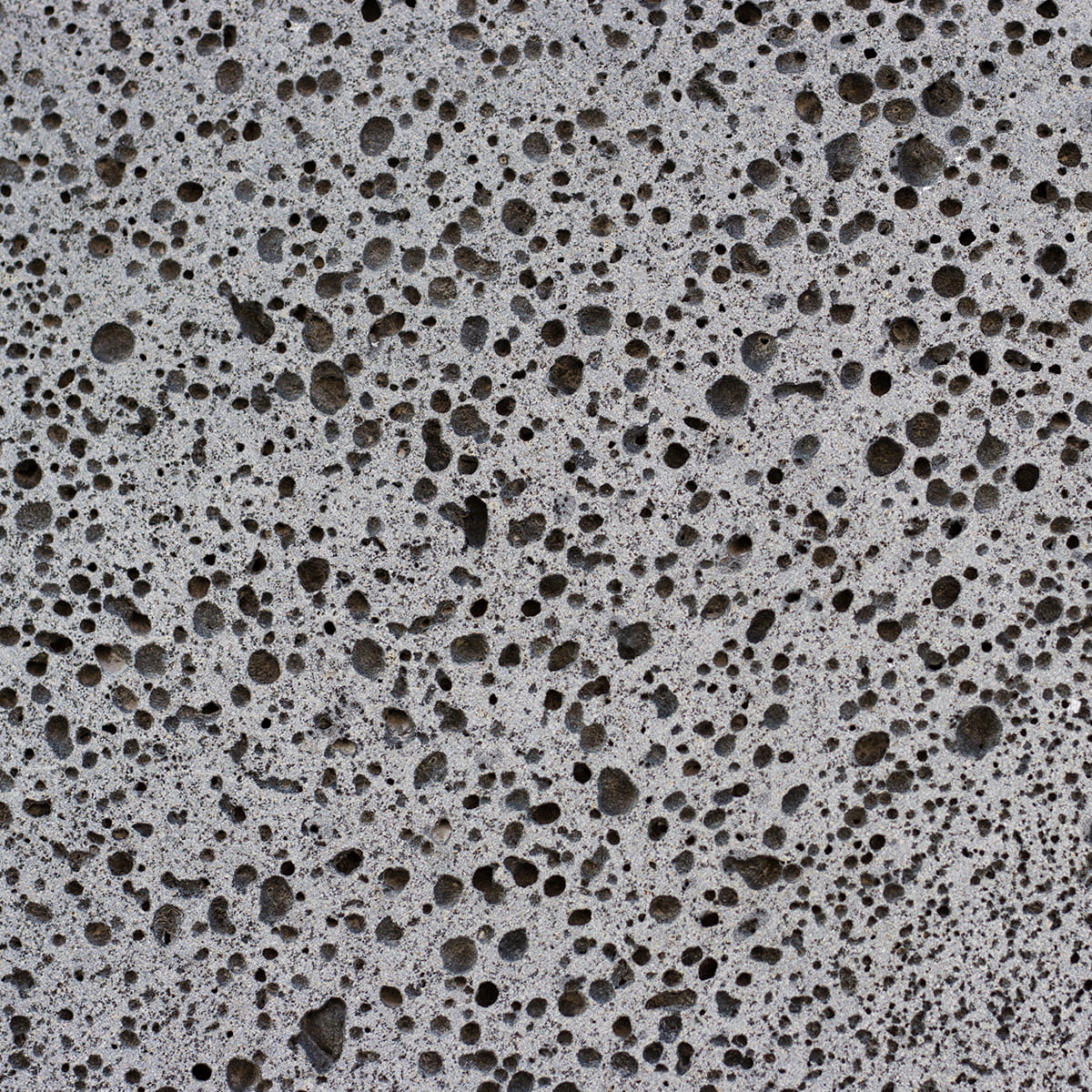
We’ve all heard about the problems with RAAC and the impact this has had on schools and other establishments across the UK, resulting in closures and disruption, particularly for teachers and pupils. RAAC was used in a wide range of buildings throughout the public and private sectors, although it tends to be more common in schools, hospitals and public buildings.
The potential for sudden structural failure is a serious cause for concern and this brief guide is designed to help you manage risks that may be associated with your buildings.
What is RAAC?
Reinforced Autoclaved Aerated Concrete was introduced into the UK post-war in the 1950s and 60s. Manufactured using fine aggregate, chemicals to create gas bubbles and heat to cure the compound, its consistency resembles an aerated chocolate bar and it was introduced as a low cost option with good thermal insulation properties. Relatively weak, with a low capacity for developing a bond with embedded reinforcement, RAAC was used in lightweight blocks for roof, wall and floor panels.
With an approximate lifespan of 30 years, problems with pre-1980 RAAC were identified in the 1990s. Since then, design standards (BS 8110 1985-20001 & EU standard EN 12602 2008) have allowed the continued use of RAAC and it has continued to be utilised as a construction option in the UK to the present day.
The problems with RAAC
The Institute of Structural Engineers (IStructE) has reported that, if properly designed, manufactured and maintained in good condition, with good bearing, RAAC installations are considered safe. However, problems with RAAC tend to occur in relation to the original materials used, intended design, manufacturing oversight and construction/installation controls.
Hazards have materialised as a result of uncontrolled modification, inadequate design, altered load forces, poor maintenance, deterioration due to age, moisture ingress and insufficient end bearing.
Over time, RAAC panels can creep and deflect, leading to:
- Water ponding on roof
- Corrosion of steel reinforcement
- Cracking, bowing of panels
- In extreme cases, sudden collapse with little warning
Actions required
Once identified, it is essential that structural engineers gauge the condition of the RAAC structure and recommend appropriate remedial measures.
We recommend you inform your insurance broker immediately on identification of RAAC and arrange an inspection/assessment by a structural engineer familiar with RAAC. (The IStructE have formed a RAAC Study Group and created a list of professionally registered structural engineers with experience of providing solutions for managing RAAC planks.)
An intrusive survey is required for effective evaluation, and an engineer will check for:
- Deflections - critical if >20mm
- Cracking - critical if there are full width cracks
- Water leaks - can increase weight and corrosion
- Debonding
- Concrete coverage depth of steel reinforcement
- Modifications after construction, including cutting and penetrations
- End bearing length - critical if <75mm
Likely Remediation Strategies:
- The addition of secondary supports or beams at the end bearing to provide an increased effective bearing length.
- Positive remedial supports to actively take the loading from the panels: this could include the addition of new timber or lightweight structures to support the panels directly. (A theatre has reportedly installed a crash deck beneath the roof to prevent RAAC falling into the theatre and thereby allowing them to continue performances).
- Passive fail-safe supports to mitigate catastrophic failure of the panels if a panel was to fail, such as a secondary structure designed to support the panels.
- Removal of individual panels and replacement with an alternative lightweight solution.
- Entire roof replacement.
Alternative Solutions
Many different and innovative solutions are available on the Internet to extend the life of affected buildings, such as the use of carbon fibre wrapping and resin injection techniques. However, not all proposed solutions may be deemed to be adequately tried and tested.
PIB recommends using caution and seeking the approval of insurers prior to commencement of any remedial works.
Action Plan
Many different and innovative solutions are available on the Internet to extend the life of affected buildings, such as the use of carbon fibre wrapping and resin injection techniques.However, not all proposed solutions may be deemed to be adequately tried and tested.
PIB recommends using caution and seeking the approval of insurers prior to commencement of any remedial works.
1. RAAC deterioration can lead to sudden collapse without warning. Arrange intrusive structural assessment immediately.
2. To ensure assessor competence, select from the IStructE’s list of professionally registered structural engineers.
3. Once RAAC issues have been identified, notify your insurance broker and review your remediation approach.
4. Prior to remedial work commencing, get insurer approval (via your broker) to ensure acceptance and prevent later issues.
5. If asbestos is identified, you're legally required to comply with Regulation 4 of the Control of Asbestos Regulations 2012.
Insurance cover - please note
Please be aware that while your building insurance policy covers damage caused by sudden and unforeseen events, most policies do not cover wear and tear or construction defects. Should RAAC failure lead to sudden damage to other parts of the building, your policy may only respond to the resultant damage. Please seek clarification and professional advice on this from your PIB representative.